ARMi N2 Generators
Nitrogen Generator
Nitrogen gas generator produces nitrogen gas from atmospheric air based on PSA (Pressure Swing Adsorption) technology. We provide variety of PSA Nitrogen gas generator, Nitrogen Plant, in all kind of industries such as Chemicals, Pharmaceuticals, Bulk Drugs, Food, Electronic Industry, Steel, Coal Mines, etc. PSA technique is simple and reliable process of separation of nitrogen gas from compressed air by adsorption of oxygen over a compact tower of carbon molecular sieves.
The “Treated” atmospheric compressed air enters an adsorption tower where it comes in contact of carbon molecular Sieves that binds the oxygen molecules and allows nitrogen to pass through void space. Pure nitrogen flows product delivery operation and once the oxygen capturing capacity in a bed is diminished the feed switches to a new adsorption tower and the old bed is regenerated through rapid depressurization and is ready for the next cycle.
WORKING PRINCIPLE
Using compressed air, Pressure Swing Adsorption (PSA) generators produce an interrupted supply of nitrogen gas. These generators use pretreated compressed air that is filtered through a carbon molecular sieve (CMS). Oxygen and trace gases get absorbed through the CMS letting nitrogen to pass through. This filtration takes place in two towers both of which contain a CMS.
When the on-line tower vents the contaminants, it is known as the regenerative mode. In this process, Oxygen, having smaller molecules gets separated from the Nitrogen and the lining in the sieve adsorbs these smaller oxygen molecules. As Nitrogen molecules are larger in size, they are unable to pass through the CMS and the result will be the desired pure Nitrogen gas.
SALIENT FEATURES
- Modular Design
• Safe & Reliable
• Hassel-free, easy to install and operate
• Completely Pre-manufactured Skids
• Fast Start-up. Fully automatic and unattended operation
• Pre-compressed bed prevents CMS bed dusting assuring maximum bed life
• Low cost on-site production
• Provide stable long term N2 Cost
APPLICATION
- Blanketing (Pharmaceuticals, Pesticides, Agriculture)
- Metal Process (Bright Annealing, PleatTreatment, Furnace)
- Laser Cutting (10bar-1000lph to 50000lph)
- Inertization Process (Chemicals, Petrochemical)
- Oil & Gas (Blanketing, Filling, Transferring)
- Food Packet( Pouch Packaging, Confectionaries)
- Laboratories (LCMS, GC)
- Tire Filling (Automobiles)
- Power Sector
- Electronics Industries
- Autoclaves Segments
- Cement Industry
ADVANTAGES
- High nitrogen purity: PSA nitrogen generator plants allow production of high-purity nitrogen from air, which membrane systems are unable to provide – up to 99.9995% nitrogen. But in most cases they do not produce more than 98.8% nitrogen with the remainder being argon that is not separated from the nitrogen by the usual PSA process. The argon is not normally a problem, as argon is more inert than nitrogen. This nitrogen purity may also be ensured by cryogenic systems, but they are considerably more complex and justified only by large consumption volumes. The nitrogen generators use CMS (carbon molecular sieve) technology to produce a continuous supply of ultra high purity nitrogen and are available with internal compressors or without.
• Low operating costs: By substitution of out-of-date air separation plants nitrogen production savings largely exceed 50%. The net cost of nitrogen produced by nitrogen generators is significantly less than the cost of bottled or liquefied nitrogen.
• Environmental impact: Generating nitrogen gas is a sustainable, environmentally friendly and energy efficient approach to providing pure, clean, dry nitrogen gas. Compared to the energy needed for a cryogenic air separation plant and the energy needed to transport the liquid nitrogen from the plant to the facility, generated nitrogen consumes less energy and creates far fewer greenhouse gases.
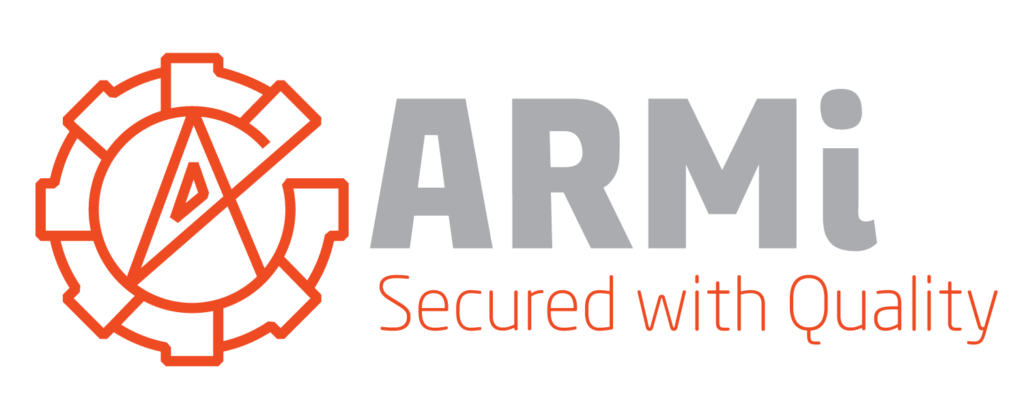
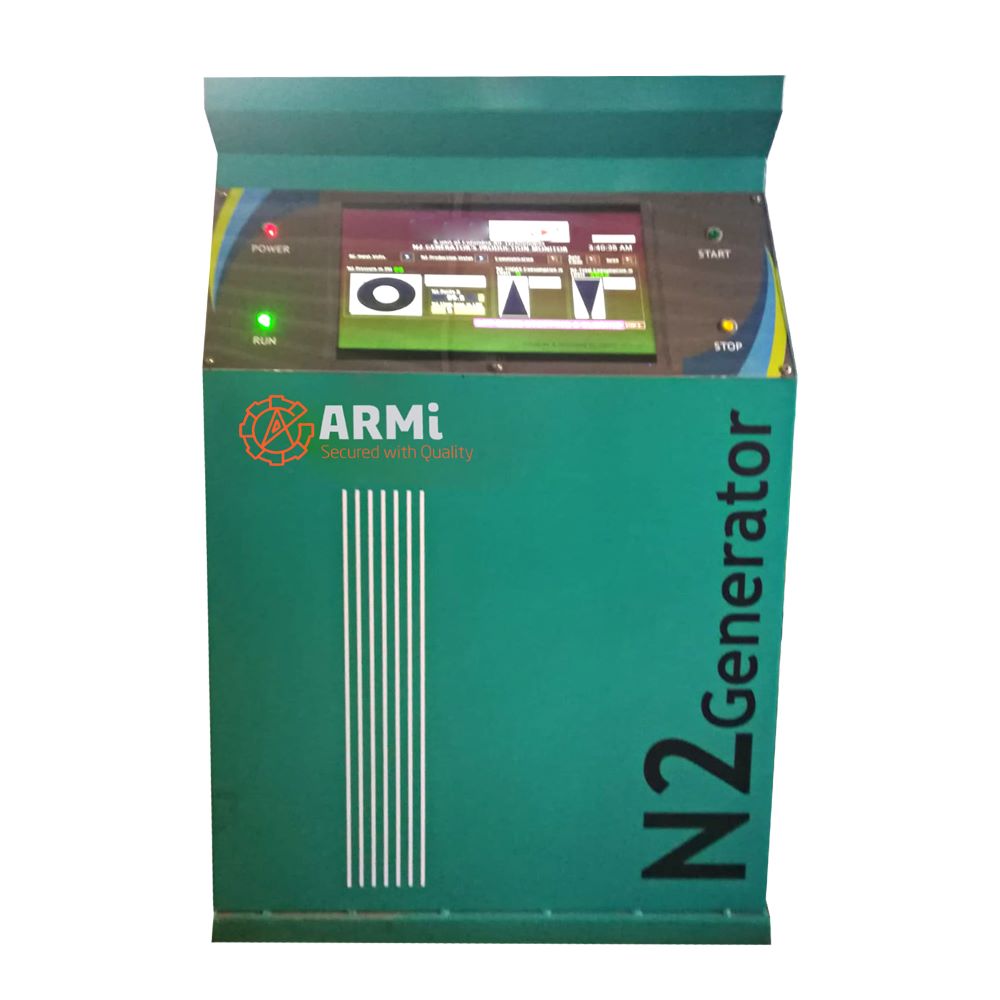